Rippengeometrien prozesssicher fertigen
Volkswagen AG – Komponenten-Werkzeugbau | Braunschweig (Niedersachsen), Deutschland
Spitzenleistung im Werkzeugbau: Negative Rippenformen zu programmieren ist nicht trivial. Gemeinsam mit OPEN MIND konnte VW am Standort Braunschweig ein sehr effizientes Programmieren von negativen Rippenformen realisieren. Zu fräsende Nuten werden automatisch erkannt, steile Bereiche und Böden getrennt bearbeitet.
Beeindruckende Fertigungstiefe. Technologischer Vorreiter. Effektivität und Effizienz in der CAD/CAM-Prozesskette. Das alles charakterisiert den Komponenten-Werkzeugbau der VOLKSWAGEN AG in Braunschweig. Hier entstehen Kokillen für Zylinderköpfe und Fahrwerksteile, Druckgießformen für Getriebe, Kupplungs- und Lenkgehäuse, Presswerkzeuge für die Dickblech-Umformung von Fahrwerksteilen und Spritzgießformen – etwa für die Stoßfänger oder Instrumententafeln aus Kunststoff.
Produktive Partnerschaft
„Wir haben uns 2002 für OPEN MIND entschieden, weil hyperMILL® unseren Ansatz der Standardisierung am besten unterstützt“, sagt Jörg Wenserski, Leiter Engineering der Maschinenzentrale. „Daraus hat sich eine produktive Partnerschaft mit OPEN MIND entwickelt, in der wir einen sehr hohen technischen Standard erreicht haben.“
Ein Beispiel liefert das Gemeinschaftsprojekt Rippenfräsen. Die Kühlrippen von Getriebegehäusen weisen sehr tiefe Kavitäten auf, die sowohl in der Programmierung als auch in der Bearbeitung einen enormen Zeitaufwand mit hohem Risiko bedeuten.
„Wir haben uns 2002 für OPEN MIND entschieden, weil hyperMILL® unseren Ansatz der Standardisierung am besten unterstützt.“
Jörg Wenserski, Leiter Engineering der Maschinenzentrale bei Volkswagen Werk Braunschweig
Rippenfräsen ohne Risiko
Die VW-Mitarbeitergruppe „Wissensmanagement-Rippenfräsen“ hatte ein Testteil erarbeitet, das alle bekannten Schwierigkeitsgrade aufwies, wie Verschachtelungen, tiefe Kavitäten, Rippenkreuzungen, radiale Rippen und Störkonturen.
Ausgehend davon entwickelte OPEN MIND einen Rippenfräszyklus, der viel Neues in den Bearbeitungsablauf brachte: eine integrierte Schrupp-/Schlichtfunktion, integrierte Taschenbearbeitung bei breiteren Rippen, eine automatische Kollisionsabdrängung des Werkzeughalters bei Berücksichtigung von konischen Fräsern und eine integrierte Bodenbearbeitung. Ein weiteres Highlight: Auch bei automatisch getrennten Bereichen kommen die Zustellparameter immer direkt aus der Werkzeugdatenbank.
Bei einem sehr hohen Verrippungsgrad konnte so die Bearbeitungszeit signifikant verkürzt werden – die reine Programmierzeit wurde durch den neuen Rippenfräszyklus halbiert. „Neben der geplanten Einsparung von Programmier- und Maschinenlaufzeit konnten wir eine höhere Prozesssicherheit und einen deutlich geringeren Werkzeugverschleiß erreichen“, sagt Wolfgang Sofftner, Ansprechpartner für die 3D-Bearbeitung im Komponenten-Werkzeugbau.
Referenz
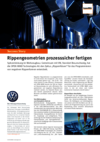
Volkswagen AG | Komponenten-Werkzeugbau
Braunschweig, Deutschland