Zu Qualität und Produktivität verpflichtet
Aerotech Peissenberg GmbH & Co. KG | Peissenberg (Bayern), Deutschland
Aerotech Peissenberg setzt auf CAD-/CAM-Systeme von OPEN MIND
Die Luftfahrtindustrie stellt hohe Ansprüche an seine Lieferanten. In besonderer Weise gilt dies für Hersteller von rotationssymmetrischen und prismatischen Komponenten, die in modernen Triebwerken zum Einsatz kommen. Dementsprechend streng sind Auflagen und Anforderungen in dieser Branche. Bei der vor rund 20 Jahren gegründeten Aerotech Peissenberg GmbH, die damals aus dem MTU-Konzern hervorging, sind sich alle Mitarbeiter des hohen Anspruchs bewusst, der an sie gerichtet ist. Neben qualifizierten Mitarbeitern bildet auch die moderne Technik eine wichtige Basis. So schafft es das Luftfahrtunternehmen, unter anderem durch den Einsatz innovativer Schrupp-Strategien aus dem Performance Pakt hyperMILL MAXX Machining von OPEN MIND die Bearbeitungszeiten diverser Bauteile um ca. 30 Prozent zu reduzieren.
„Als Beta-Tester sind wir immer sehr nah dran an den Neuentwicklungen in hyperMILL und erleben, wie schnell und qualifiziert das Unternehmen arbeitet. Dementsprechend fühlen wir uns sehr gut aufgehoben.“
Hermann Stork, Leiter NC-Programmierung bei ATP
Zu den Kernkompetenzen des innovativen Unternehmens zählen die komplexe mechanische Bearbeitung, Oberflächenveredelung und Prüfung diverser sicherheitskritischer Bauteile mit bis zu 1.250 mm Durchmesser, die aus schwer zerspanbaren Legierungen bestehen. Zum Einsatz kommen diese laut Tolga Bayraktar, Leiter Technik bei Aerotech Peissenberg, in fast allen neuen Mehrstufen-Triebwerken. Der Luftfahrt-Ingenieur ergänzt dazu: „Das gibt mir ein Gefühl von Sicherheit, wenn ich selbst als Passagier in einem Flugzeug sitze. Denn in fast jedem Passagierflugzeug weltweit sind sicherheitsrelevante Teile von uns verbaut.“
Doch nicht allein wegen des umfangreichen Know-hows im Bereich der Produktion sind die Experten von ATP gefragt. Ihr Wissen wird bei neuen Bauteilen schon im Entwicklungsstadium angezapft, wie Tolga Bayraktar erklärt: „Die Design-Ideen für Triebwerksteile kommen natürlich von unseren Kunden. Im Hinblick auf eine fertigungsgerechte Konstruktion ist aber die Erfahrung unserer Mitarbeiter von entscheidender Bedeutung.“ Letztlich geht es nicht nur um die Funktionalität der Blisks, Impeller, Spulen, Ringe, Gehäuse etc.. Ebenso wichtig ist die zeitgerechte Herstellung zu vertretbaren Kosten – also das sogenannte „Design to cost“. Genau hierzu tragen die Konstrukteure von Aerotech mit ihrem Wissen um optimale Produktionstechnologien und -prozesse bei.
ATP bietet ein breites Technologiespektrum
Ist die Entwicklung abgeschlossen und damit das Design eines Bauteils verabschiedet sowie der Auftrag erteilt, macht man sich in Peißenberg an die Umsetzung. Das benötigte Rohmaterial wird bestellt und sämtliche Fertigungsprozesse als interne und externe Supply Chain festgelegt. Hilfreich hierbei: das breite Technologiespektrum von ATP. Es reicht vom CNC-Drehen und -Fräsen über kombinierte Bearbeitungstechnologien und das Räumen bis hin zum Wuchten, Plasmastrahlen, Ätzen, Reinigen, Rissprüfen, Kennzeichnen und hochgenauen Messen.
Um einen effizienten Herstellungsablauf gewährleisten zu können, investiert der Triebwerkszulieferer regelmäßig in neue Maschinentechnik. Zum Einsatz kommt diese primär bei Neuprodukten oder wenn deutliche Produktivitätsgewinne zu erwarten sind. Hintergrund dazu: Sämtliche Prozesse, Maschinen, Werkzeuge etc. werden nach der Abnahme durch den Kunden „eingefroren“. Etwaige Verbesserungen erfordern eine erneute, aufwändige Abnahme, die Zeit und Geld kostet. Für den erfahrenen Luftfahrt-Experten Bayraktar eine Selbstverständlichkeit: „Teilesicherheit ist nirgendwo so wichtig wie in der Luftfahrt. Daher ist klar, dass unsere Kunden eine hundertprozentige Prozess-Transparenz brauchen und wir sie gewährleisten.“
Die seit Jahren positive Umsatzentwicklung von ATP lässt auf eine hohe Kundenzufriedenheit schließen. Insbesondere in punkto Know-how, Qualität und Zuverlässigkeit bekommt das Unternehmen stets positives Feedback. Einzig bei den Kosten sieht Tolga Bayraktar standortbedingt gewisse Nachteile für Aerotech Peissenberg: „Die Löhne sind hier deutlich höher als in Fernost. Aber mit den kreativen Ideen und dem Know-how unserer Mitarbeiter und Partnerfirmen gleichen wir das wieder aus. Dadurch sind wir mehr als wettbewerbsfähig.“
Optimierte CAM-Programmierung erhöht Fertigungsproduktivtät
Als beispielhaft nennt der Technikchef diverse Verbesserungen im Bereich der CAM-Programmierung, die auf der guten Zusammenarbeit seiner Programmierer mit den Experten der OPEN MIND Technologies AG, Weßling, basieren. Was vor rund zehn Jahren mit ersten Anwendungen von hyperMILL CAD (ehem. hyperCAD-S) und hyperMILL begann, hat sich inzwischen auf nahezu alle Programmierarbeiten für Fräsmaschinen ausgedehnt und wird sukzessive auch für die Fräs-Dreh- und Drehbearbeitung eingeführt. Hilfreich erscheint hier unter anderem die gute Anbindung von hyperMILL an die Werkzeugverwaltungs- sowie an die Unternehmensplanungs-Software.
Außerdem freut sich Hermann Stork, Leiter NC-Programmierung bei ATP, über das hohe Innovationspotenzial bei OPEN MIND: „Als Beta-Tester sind wir immer sehr nah dran an den Neuentwicklungen in hyperMILL und erleben, wie schnell und qualifiziert das Unternehmen arbeitet. Dementsprechend fühlen wir uns sehr gut aufgehoben.“
Um zu prüfen, ob die jüngsten Optimierungen in der Praxis etwas bringen, hat Aerotech Peissenberg mehrere Vergleichstests durchgeführt. So wurde beispielsweise die Schruppbearbeitung von Gehäuseteilen aus hochlegiertem Stahl mit und ohne das High-Performance-Cutting-Modul des hyperMILL MAXX Machining Pakets programmiert. Ergebnis: Die Bearbeitungszeit konnte um ca. 30 Prozent reduziert werden. Ähnliche Einsparungen haben sich mit der verbesserten Frässtrategie bei einem Kegel aus Pulvermetall realisieren lassen.
Das Geheimnis des hyperMILL MAXX Machining-Schruppmoduls liegt in der intelligenten Aufteilung von spiralförmigen und trochoidal ähnlichen Werkzeugwegen sowie in der dynamischen Anpassung des Vorschubs an die jeweiligen Schnittbedingungen. So lässt sich ein maximales Zeitspanvolumen erreichen. Dabei kann das leistungsstarke HPC-Schruppmodul laut Andreas Leser, Vertriebsleiter Deutschland bei OPEN MIND, für alle Bearbeitungsarten eingesetzt werden – also für 2D-,3D- und 5-Achs-Operationen. Er ergänzt dazu: „Unsere Kunden profitieren auch von unserer Vorreiterrolle bei der 5-Achs-Technologie. Denn mit hyperMILL® lassen sich auf einzigartige Weise auch gekrümmte Bauteile 5-achsig fertigen.“
Sehr zufrieden ist Hermann Stork mit der einfachen Bedienbarkeit von hyperMILL CAD. Weiterhin stellt er fest: „In der aktuellen Software steckt unheimlich viel Potenzial. Nach einer Woche CAD-, einer Woche Fräs- und drei Tagen Dreh-Training bin ich bestens für nahezu alle Eventualitäten vorbereitet.“
Neue Funktionen für hyperMILL CAD und hyperMILL
Die enge partnerschaftliche Zusammenarbeit zeichnet sich auch dadurch aus, dass weitere neue Funktionen in hyperMILL CAD und hyperMILL diskutiert und angepasst werden. Dazu zählen unter anderem neue Drehfunktionen und eine optimierte Vorschubbegrenzung beim Fräsen. Ähnlich unkompliziert soll laut Hermann Stork künftig das Fräsen mit Winkelköpfen werden.
Sehr zufrieden ist Hermann Stork mit der einfachen Bedienbarkeit von hyperMILL CAD. Weiterhin stellt er fest: „In der aktuellen Software steckt unheimlich viel Potenzial. Nach einer Woche CAD-, einer Woche Fräs- und drei Tagen Dreh-Training bin ich bestens für nahezu alle Eventualitäten vorbereitet.“
Galerie
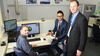
V.l.n.r.: Hermann Stork, NC-Programmierer, und Tolga Bayraktar, Leiter Technik bei ATP freuen sich gemeinsam mit Andreas Leser, Vertriebsleiter Deutschland bei OPEN MIND, über die erfolgreiche Zusammenarbeit und darüber, dass mit dem Schruppmodul hyperMILL® MAXX Machining einige Bauteile von ATP um mehr als ein Drittel produktiver hergestellt werden können.
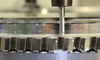
…Dieses wird vom Postprozessor übersetzt und via Netzwerke an die Maschine übertragen. In mehreren Iterationsschleifen optimieren die NC-Experten von Aerotech Peissenberg die Bauteil-Programme bis zur Endabnahme beim Kunden. Nach finaler Freigabe dürfen am gesamten Produktionsprozess keine Änderungen mehr erfolgen.