Schnell programmiert und sicher fünfachsig zerspant
Institut für Robotik und Mechatronik (DLR-RM) | Oberpfaffenhofen, Bayern
Simultane 5-Achs-Bearbeitung – nur wenn es nicht anders geht, so hieß es jahrelang in der mechanischen Fertigung des Instituts für Robotik und Mechatronik im Deutschen Zentrum für Luft- und Raumfahrt (DLR). Mit der Einführung der CAD/CAM-Software hyperMILL von OPEN MIND inklusive der Simulationstechnologie VIRTUAL Machining und der Funktion BEST FIT hat sich das geändert. Denn damit erzeugen die Zerspanungsspezialisten in kurzer Zeit optimierte 5-Achs-NC-Programme, die nach NC-Code-Simulation sicher auf Kollisionsfreiheit geprüft sind. Dank hyperMILL BEST FIT lassen sich auch 3D-gedruckte Bauteile einfach und schnell aufspannen sowie präzise bearbeiten.
Auf dem DLR-Gelände in Oberpfaffenhofen bei München ist unter anderem das Institut für Robotik und Mechatronik, kurz DLR-RM, untergebracht. Hier arbeiten Forschungsteams und Studierende an Roboterarmen, -händen und -greifern. Sie entwickeln mehrarmige Systeme und mobile Plattformen, die andere Planeten, Kometen und Asteroiden erkunden, Bodenproben nehmen etc. Besonders beindruckend sind die weitgehend autonomen Flug- und Laufroboter sowie humanoide Roboter, wie zum Beispiel TORO, der humanoide Laufroboter. Mit ihm forschen die Wissenschaftler an der Umsetzung zweibeiniger, dynamischer Fortbewegung: TORO lernt derzeit robustes Gehen, Treppensteigen und vieles mehr.
„Die Investition in hyperMILL samt VIRTUAL Machining und BEST FIT hat sich auf jeden Fall gelohnt. Wir sind schneller beim Programmieren, wir erhalten eine NC-Code-Simulation, die uns größtmögliche Sicherheit gibt, und können unsere gedruckten Bauteile viel einfacher einrichten.“
Michael Dreer, Feinmechaniker am DLR-RM
Die Roboter werden hier nicht nur entwickelt, sondern auch gebaut
Michael Dreer ist Feinmechaniker am DLR-RM. Er erklärt, dass die hier entwickelten Robotersystem nicht nur in der Luft- und Raumfahrt eingesetzt werden, sondern auch in der Medizintechnik, in Service und Pflege sowie in der modernen Industrie. „Wir betreiben hier Grundlagenforschung, aber anhand von konkreten Projekten, oft mit Partnern aus der Industrie, aber auch in Eigenregie“, sagt Dreer und weist darauf hin, dass das DLR-RM neben Roboterkinematiken auch Systemkomponenten wie zum Beispiel besonders klein- und leichtbauende Motore, Bildverarbeitungssysteme, Bediengeräte etc. und vielerlei Software entwickelt.
„Nicht nur entwickelt“, betont Dreer. „Wir haben hier eine sehr hohe Fertigungstiefe und stellen alle anspruchsvollen Teile für unsere Roboter selbst her.“ Zusammen mit seinen 6 Kollegen ist er für die komplette mechanische Fertigung im Institut zuständig. Eine Aufgabe, die eine frühzeitige, enge Zusammenarbeit mit den Konstrukteuren erfordert, wie Dreer erwähnt: „In unseren Bauteilen ist Elektronik und Mechanik auf engstem Raum verbaut. Jedes Bauteil muss so gestaltet sein, dass es – bei aller Komplexität – auch vernünftig gefertigt werden kann.“ Jeder Fertigungsspezialist betreut ein Bauteil komplett durch die Prozesskette, von der Werkzeug- und Materialbestellung, über die Programmierung bis zur Zerspanung und Qualitätssicherung.
Michael Dreer ist schon seit fast 30 Jahren beim DLR-RM und hat in dieser Zeit große Fortschritte in der Robotertechnik miterlebt: „Gerade im Leichtbau gab es immer wieder Entwicklungsschritte, die auch an unsere Fertigungstechnik wachsende Ansprüche gestellt haben.“ Um Schritt halten zu können, investierte das DLR-RM erst vor einigen Jahren in mehrere 5-Achs-Bearbeitungszentren, in eine Dreh-Fräsmaschine mit angetriebenen Werkzeugen und in ein Kombi-BAZ, das Drehen und Fräsen gleichermaßen beherrscht. Insbesondere durch die simultane 5-Achs-Bearbeitung wurden auch in der CAD/CAM-Ausstattung Veränderungen notwendig.
CAM-System für modernste Zerspanungstechnologie
Ist unsere CAD-Software noch zeitgemäß? Wie steht es um das bisher im CAD-System integrierte CAM-Modul? Genügt es den zukünftigen Anforderungen? Die Verantwortlichen stellten sich diese Fragen und kamen zu dem Schluss, dass die CAM-Programmierung unabhängig vom CAD-System der Konstrukteure sein sollte. „Wir brauchen hier in der mechanischen Fertigung eine CAM-Software, die den Datenaustausch mit sämtlichen CAD-Systemen beherrscht und die uns bei der simultanen Mehrachsbearbeitung sowie bei Dreh-Fräszentren unterstützt. Zudem muss sie uns hohe Prozesssicherheit bieten“, fasst Michael Dreer zusammen.
Bei der Suche nach einem solchen zukunftsfähigen CAM-System rückte schon bald hyperMILL von OPEN MIND in den Fokus. „Diese Software ist sehr praxisnah und bietet leistungsstarke Technologien. Man merkt, dass sie von Leuten entwickelt wurde, die selbst Erfahrung in der Zerspanung haben und mit der Problematik komplexer Bauteile vertraut sind“, sagt Harald Wagner, Gruppenleiter der Mechanischen Fertigung. „Das wird vor allem in der einfach zu verstehenden Programmieroberfläche deutlich, auch im 5-Achs-Bereich.“
Die große Auswahl an schnell und einfach programmierbaren 5-Achs-Funktionen war ein wichtiges Argument pro hyperMILL. Denn die Außenstrukturen von DLR-Robotern weisen sphärische 3D-Oberflächen auf, haben außerdem Fixierungen und Flansche in vielen Ausrichtungen sowie Hinterschnitte, so dass die Bearbeitung oft nur fünfachsig zu bewältigen ist. „Die 5-Achs-Programmierung war bei unserem bisherigen System nur mit großem Aufwand zu bewältigen. Das hatte zur Folge, dass wir nur dann fünfachsig frästen, wenn es gar nicht anders ging“, berichtet Dreer.
Das ist jetzt anders. Seit etwa drei Jahren arbeitet Michael Dreer mit hyperMILL als erster seiner Abteilung. „Das bot sich an, da ich mich vor allem mit komplexen 5-Achs-Teilen beschäftige“, sagt der erfahrene Feinmechaniker. Inzwischen ist ein weiterer Kollege auf hyperMILL umgestiegen und die anderen werden nach und nach folgen.
Zu den Stärken von hyperMILL zählt Dreer die umfangreiche, integrierte Werkzeugdatenbank, die es ermöglicht, sämtliche Werkzeuge fürs Bohren, Fräsen und Drehen zentral zu verwalten. In ihr lassen sich Drehzahl- und Vorschubwerte, individuelle Technologiewerte für Materialien und selbst Anwendungsfälle speichern. „Ich war zwar eine Weile beschäftigt, bis ich alle Werkzeugdaten eingepflegt hatte. Aber dafür spare ich mir jetzt sehr viel Zeit bei der Programmierung und Werkzeugauswahl. Zudem profitiere ich von optimalen Prozessen dank verlässlicher Technologiedaten“, erwähnt Dreer.

Michael Dreer, Feinmechaniker am DLR-RM: „Die CAD/CAM-Software hyperMILL von OPEN MIND ist sehr praxisnah und bietet leistungsstarke Technologien. Man merkt, dass sie von Leuten entwickelt wurde, die selber Erfahrung in der Zerspanung haben und mit der Problematik komplexer Bauteile vertraut sind.“
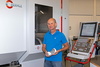
Michael Dreer, Feinmechaniker am DLR-RM: „Die Investition in hyperMILL samt VIRTUAL Machining und BEST FIT hat sich auf jeden Fall gelohnt. Wir sind schneller beim Programmieren, wir erhalten eine NC-Code-Simulation, die uns größtmögliche Sicherheit gibt, und können unsere gedruckten Bauteile viel einfacher einrichten.“
Unverzichtbar: die NC-Code-Simulation
Für große Begeisterung sorgt bei Dreer hyperMILL VIRTUAL Machining (VM), das er ein Jahr später ergänzte: „Damit habe ich von OPEN MIND ein Gesamtpaket, das mir perfekte NC-Codes generiert und über eine präzise NC-Code-Simulation eine nahezu hundertprozentige Kollisionsfreiheit gewährleistet.“
NC-Code-Simulation ist in der mechanischen Fertigung des DLR-RM nichts Neues. Dreer und seine Kollegen erachten sie beim fünfachsigen Bearbeiten für zwingend notwendig: „Die Gefahr einer Kollision mit schwerem Schaden ist einfach zu groß. Selbst ein versierter, praxiserprobter Programmierer kann nie sicher vorhersagen, wie die Bewegung auf der Maschine tatsächlich aussieht. Wenn man mit reinen CAM-Daten simuliert, ist das nicht ausreichend.“ Daher nutzten Dreer und seine Kollegen schon seit Jahren eine separate Simulationssoftware zur NC-Code-Simulation.
Diese kam anfangs auch mit hyperMILL zum Einsatz. Für Dreer ein Fortschritt: „Gegenüber der bisherigen CAM-Software bietet hyperMILL eine bessere Schnittstelle und einfachere Datenübergabe. Aber seit wir über die NC-Code-Simulation des VIRTUAL Machining Centers verfügen, geht alles noch viel schneller. Jetzt haben wir einen durchgängigen Workflow, da hyperMILL alle prozessrelevanten Daten automatisch zur Verfügung stellt. In kürzester Zeit bekomme ich ein Feedback, ob das Programm an der Maschine kollisionsfrei läuft oder nicht – mit nahezu hundertprozentiger Sicherheit.“
Die Unterstützung durch hyperMILL und der virtuellen Maschine ist den Fertigungsspezialisten des DLR-RM nicht nur beim fünfachsigen Fräsen wichtig. Auch das Programmieren des Dreh-Fräszentrums ist eine anspruchsvolle Aufgabe, die durch hyperMILL TURN-MILL Machining unterstützt wird. Michael Dreer fügt noch hinzu: „Um auch hier maximale Sicherheit zu erhalten, haben wir uns als Betatester für VM für das Dreh-Fräsen zur Verfügung gestellt, was mittlerweile top zuverlässig funktioniert.“
Automatisiertes Job Linking und BEST FIT
Zum hyperMILL VIRTUAL Machining gehört neben der NC-Code-Simulation auch das Modul Optimizer. Dieses passt während der NC-Code-Generierung das NC-Programm perfekt an die kinematischen Eigenschaften der gewählten Maschine an – vollautomatisch. Dabei werden die besten technischen Anstellungen gewählt und optimierte Verbindungsbewegungen zwischen einzelnen Operationen erstellt. Michael Dreer nutzt den Optimizer vor allem für das Job Linking: „Diese Funktion verknüpft meine einzelnen Jobs mit sicheren optimierten und kollisionsfreien Bewegungen, ohne dass ich mich darum kümmern muss.“
Während das Fertigungsteam des DLR-RM mit dem Optimizer Programmierzeit spart, verkürzt die Funktion BEST FIT, die als Add-on für hyperMILL VIRTUAL Machining erhältlich ist, die Zeit fürs Aufspannen und Ausrichten des Bauteils. „Bei unseren Leichtbaustrukturen hatten wir früher über 90 Prozent Zerspanungsvolumen, weshalb wir heute diese Bauteile nach Möglichkeit im 3D-Metalldruck oder Feinguss herstellen lassen“, erklärt Michael Dreer. „Funktionsflächen, Bohrungen und Gewinde müssen wir aber auch an diesen Teilen zerspanen.“
Eine Schwierigkeit bei diesen additiv erzeugten oder gegossenen Teilen lag im Aufspannen auf der Maschine und dem exakten Ausrichten. Das erforderte zum einen komplizierte Spannmittel und einen enormen Zeitaufwand, da ja auch eine Reproduzierbarkeit bei Nachfolgeteilen erreicht werden sollte. „Mit hyperMILL BEST FIT haben wir eine Möglichkeit bekommen, solche Teile einfach und schnell einzurichten sowie prozesssicher zu zerspanen“, freut sich Harald Wagner.
Bei BEST FIT handelt es sich um eine intelligente Bauteilausrichtung im CAM-System. Das heißt, das Bauteil wird unausgerichtet auf der Maschine fixiert. „Wir nutzen dafür zum Beispiel kostengünstige, gedruckte Kunststoffvorrichtungen“, erwähnt Michael Dreer, „da es beim Spannen nicht auf den Millimeter ankommt.“ Dann wird das Bauteil auf der Maschine mit einem 3D-Messtaster erfasst. Die Ergebnisse werden als Messprotokoll zurück ans CAM gesendet. Anschließend verschiebt hyperMILL BEST FIT das CAD-Bauteil so, dass es sich komplett im gemessenen Rohteil befindet. „Ich kann das am Bildschirm kontrollieren, aber in der Regel passt das auf Anhieb perfekt.“ Dann modifiziert BEST FIT den NC-Code entsprechend, simuliert ihn hinsichtlich der tatsächlichen Aufspannsituation und optimiert das Programm automatisch. Michael Förster, Senior Product Marketing Manager bei OPEN MIND, erklärt das weitere Vorgehen: „Um eine sichere und exakte Bearbeitung zu gewährleisten, führt der Maschineneinrichter nun eine Verifikationsmessung durch. Stimmt die Position auf der Maschine mit dem optimierten Programm überein, kann die Bearbeitung starten, ohne dass er das Bauteil auf der Maschine aufwendig rausrichten musste. Die Vorteile: ein immenser Zeitgewinn, sichere Bearbeitung und planbare Prozesse.“
Michael Dreer und Harald Wagner stimmen dem voll und ganz zu: „Damit sparen wir uns sehr viel Aufwand. Die Investition in hyperMILL samt VIRTUAL Machining und BEST FIT hat sich auf jeden Fall gelohnt. Wir sind schneller beim Programmieren, wir erhalten eine NC-Code-Simulation, die uns größtmögliche Sicherheit gibt, und können unsere gedruckten Bauteile viel einfacher einrichten.“