Create the Future of Manufacturing Together
hyperMILL® – your crucial piece for your connected manufacturing environment!
“Talent wins games, but teamwork and intelligence win championships,” Michael Jordan once said. Today, modern manufacturing is unthinkable without a powerful CAM system that smoothly interfaces with all your software solutions to help make your business succeed.
A CAM system is a basic requirement for creating NC programs for your CNC machines. And if you want to achieve a seamless flow of information and leverage synergies, the CAM system must be capable of more: It must also connect with other systems and areas.
This is exactly what hyperMILL® does, because it perfectly connects with all important processes across the various manufacturing areas through integrations, interfaces and built-in innovations. So stop compromising and connect your manufacturing with the best systems using hyperMILL®! We support you in planning and implementing your digital manufacturing environment according to your specific requirements.
Click through our connected manufacturing topics!
Download our e-paper
CAM system for a connected world
What is the role of the CAM system in a connected world of the future?
Get benefits from hyperMILL®
We can help you identify the areas of your manufacturing operations that will benefit from interfacing with hyperMILL®.
We will collaboratively plan a digital manufacturing environment fully aligned with your individual requirements.
Customer Interviews
BÖLLHOFF: PLM System
Customer Interview
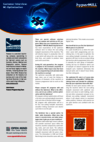
Tonasco:
NC optimization
Customer Interview
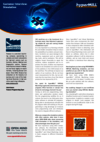
Tonasco: Simulation
Customer Interview

Henkel Modellbau:
SHOP-Viewer
Customer Interview
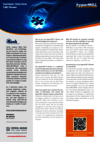
Koch: CAD Viewer
Customer Interview