MES-sharp Analysis
Key Questions for Individual MES Success
11.03.2024 — A Manufacturing Execution System (MES) can free manufacturers from unproductive processes, activities, and errors. It can control processes in real time and make them transparent at a glance whilst integrating heterogeneous automation landscapes. MES solutions are as diverse in practice as company requirements, and there are a number of questions that need to be answered.
Which manufacturing scenarios benefit from a MES?
The use of a MES is generally recommended for all industries and company sizes. The systems demonstrate their particular strengths in companies that have a wide variety of components in single-part and small-batch production. When production becomes more complex and frequent, set-up changes are required. This applies to machining production and also to special-purpose machine construction, where many thousands of parts have to be procured or manufactured over a long period of time and must be incorporated into the production workflow or schedule.
In contrast, small single-part contract manufacturers with just a few employees can also benefit from a MES. This is because the owners of these companies often fulfill many tasks at the same time and they need remote access that provides an overview of free capacity or clarity as to if or where something may be going wrong.
Wouldn’t an ERP system be enough?
The focus of an ERP system is on a company’s organization and commercial processes, not on manufacturing. ERP software is usually unable to automatically map highly dynamic production control with frequent changes. It often requires manual intervention. As a result, many companies have failed when trying to use an ERP system for these purposes. However, ERP and MES can be connected and data can be imported and exported, and synergies can be created.
How does a MES improve production planning and control?
A production manager needs to be able to get an overview at all times. This includes an insight of what is currently happening on a machine, which tool is running and where, and also which NC program is available and where. This also includes knowing what stage a machining process is in, without having to take a tour of the production facility. It is even more important to know where something is missing or is not being manufactured in line with the plan. Employees should also be able to avoid wasting valuable time searching for information or material. It is precisely these types of unproductive activities and processes that create excessive throughput times that lead to long lead times. Calculations have shown that a toolmaking company with 25 employees loses the capacity of two man years on average as a result of such inefficiencies.
An agile MES with automatic production and machine data acquisition (PDA/MDA) prevents or limits this. It also ensures that all necessary data, materials, equipment, and the associated personnel are available at the right place and at the right time. It makes planning and ongoing processes visually transparent in real time via a dashboard and immediately displays errors and deviations. The comprehensive digitalization and connectivity save time from being spent on manual processes and keeping paper records. Order planning is also simplified as free capacities or overloads are visible at a glance.
What needs to be integrated?
In many companies, various systems, including in-house developments determine the IT production landscape. The aim of a MES should be to integrate all important existing IT modules. This applies to automation software, NC programs, CAD/CAM systems and also to ERP, PDM/PLM and other software. This is the only way to plan and control production with maximum efficiency and automation and develop it for Industry 4.0. However, individual MESs differ greatly in terms of their integration capability, this is also the case when it comes to incorporating future technologies.
What are the benefits of CAD/CAM integration, for example?
A CAD/CAM solution like hyperMILL® is a crucial component for connected manufacturing and a key source of data. It is therefore extremely important that this data reaches the respective workstation in a reliable manner. A manufacturer of injection molds would previously save the NC programs from the CAM system in directories on the server and manually transfer them from the server to the controller one at a time. Now, the digital NC program management of the MES reliably transfers the NC data to the corresponding machine at the touch of a button. The MES also controls external NC program simulation. The process and data flow is fully automated. This means that 100 percent of the NC programs are now simulated – not just random samples as before. This makes production significantly safer, especially when dealing with an automation system.
Effort and risks?
Manufacturing companies have very different needs. Modular, agile MES solutions like Hummingbird MES and customized implementation projects meet these needs. The solutions can range from an individual starter package with commissioning in the shortest possible time and without a consulting budget to a comprehensive overall solution with support. Some MES solutions do not require any installation and so speed up the whole process. Examples of the successive expansion of an MES show how it can work. One company started with a basic MES package for production planning and synchronized production control, including PDA/MDA and ERP integration. Over the course of several years, the company gradually established a holistic production management system with CAM integration and central tool management, among other things.
When introducing an MES, it may be necessary to reorganize existing work processes. It is therefore important in advance to get the relevant parties and employees on board and involved with the necessary changes. This will allow the various experts to give their respective views on future MES requirements.
MES is becoming more important
In the future, the world of production will be determined by increasing digitalization, volatility, and automation with more individual products and smaller batch sizes. A MES can provide the required flexibility and solutions that offer both greater efficiency and production reliability. It is important not to forget this key point: Where there is a shortage of skilled workers, an MES can make work easier for existing employees and give them the time they need to cope with additional work.
Author: Marcus Kalbacher, Consultant MES at OPEN MIND Technologies AG
Photos: Hummingbird
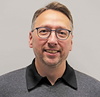
Do you have questions about the special Hummingbird modules for the hyperMILL® CAM software?
Do you want to know how to optimize your manufacturing management?
If so, contact OPEN MIND at Info.UK@misaificaopenmind-tech.com