CAM Software for the Watches and Jewelry Industry
Maximum precision, excellent surface quality, and the best possible process reliability.
CAM systems have become indispensable to the watch and jewelry industry. They are used to manufacture microparts (within the scope of micromechanics) as well as intricate pieces of jewelry. They allow manufacturing companies to benefit from many advantages, such as high levels of flexibility and process reliability.
For manufacturing companies, producing delicate precision pieces for premium watches or jewelry is not an easy task. This calls for many microscopically small milling parts produced in large series at a consistently high level of quality. That is why NC programmers from the watch and jewelry industry place specific requirements on their CAM systems: They need maximum precision, excellent surface quality, and the best possible process reliability.
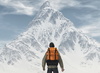
Industry Challenges
-
Reduce machining times
Through innovative HSC and HPC strategies for roughing and finishing
-
Reduce programming times
Through automated NC programming for pockets and holes thanks to feature and macro technology
-
Maximum process reliability
Thanks to collision-checked toolpaths and reliable simulation technology
-
Optimal surface quality
Blending strategies minimize additional finishing processes
5‑axis Machining: Tiara | Oyama Engineering
This video shows the machining of a tiara in cooperation with Oyama Engineering. This part represents superb surface quality, smallest details and highest precision.
Precise and reliable like a premium clock
When it comes to clockwork components made from platinum, steel, brass, titanium, or other premium materials, hyperMILL® makes it possible for NC programmers to produce precision parts in an efficient, accurate, and reliable way. Highly developed 5‑axis machining strategies make it possible to manufacture complex free-form surfaces as well as time-consuming engravings in just a single process. The result: impressive milling results with outstanding surfaces that significantly reduce the effort required for time-consuming additional finishing processes.
Would you like to learn more about our complete CAM solution for the Watches and Jewelry Industry?
If so, please contact OPEN MIND Technologies USA, Inc.
1492 Highland Avenue, Unit 3, Needham MA 02492
CAM Strategies for Industry-specific Components
Automation
5‑axis Machining
Feature and macro technology
The feature recognition in hyperMILL® makes it possible to identify the constructive properties of a component; for example, all holes including the corresponding manufacturing information.
Predefined programming macros use this information and thereby enable automated programming of the machining operations.
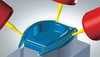
5‑axis drilling
The 5‑axis drilling function allows drilling jobs with different tool angles to be programmed simply and quickly. All the necessary positions are independently calculated by this milling strategy, and all lead-in points are connected with one another in a path-optimized and collision-checked way.Time is a scarce commodity
For watchmakers, time is, naturally, a particularly important factor. Optimized processes are the best means of saving time. hyperMILL® offers many solutions to develop efficient processes. Feature and macro technology as well as custom automation make it possible to save precious programming time. Powerful simulation solutions can minimize set-up times. Moreover, reducing the amount of follow-up work also always means shorter machining times and therefore reduced costs.
Advantages at a Glance
-
Complete machining
All machining strategies are integrated in a single user interface
-
High degree of automation
From feature and macro technology through to fully automated NC programming
-
High process reliability
Perfect milling paths as well as reliable simulation and collision avoidance
-
Easy to program
Intuitive and supported by automated functions
-
High-end postprocessors
Optimally tailored to the customer’s requirements