Quickly Programmed and Safely Machined on Five Axes
Institute of Robotics and Mechatronics (DLR-RM) | Oberpfaffenhofen, Germany
Simultaneous 5-axis machining – only if there is no other way. For years,this was the motto in mechanical production at the Institute of Robotics and Mechatronics at the German Aerospace Center (DLR). This changed with the introduction of the hyperMILL® CAD/CAM software and its VIRTUAL Machining simulation technology and BEST FIT function from OPEN MIND. The machining specialists use it to generate optimized 5-axis NC programs in a short time that are reliably checked for collisions after NC code simulation. Thanks to hyperMILL® BEST FIT, 3D-printed components can also be clamped quickly, easily and machined precisely.
The DLR site in Oberpfaffenhofen near Munich is where research teams and students work on robotic arms, hands, and grippers. They develop multi-arm systems and mobile platforms that explore other planets, comets, and asteroids, take soil samples, and so on. Particularly impressive are the largely autonomous aerial and legged robots as well as humanoid robots, such as TORO, the humanoid walking robot that scientists are using to research the implementation of bipedal, dynamic movement. TORO is currently learning robust walking, climbing stairs, and much more.
“The investment in hyperMILL® VIRTUAL Machining and BEST FIT has definitely paid off. We are faster at programming, we get an NC code simulation that gives us the greatest possible safety, and we can set up our printed components much more easily.”
Michael Dreer, Precision Mechanic at DLR-RM
The robots are developed & built here
As a precision mechanic at DLR-RM, Michael Dreer explains that the robot systems are not only used in the aerospace industry, but also in the medical device industry, service and care, as well as in modern industry. “We carry out basic research on the basis of specific projects, often with partners from industry, but also on our own initiative,” says Dreer, pointing out that in addition to robot kinematics, DLR-RM also develops system components. This includes small lightweight motors, image processing systems, operating devices plus a wide range of software.
“Not just developed,” emphasizes Dreer. “We have a very high level of vertical integration here and manufacture all the sophisticated parts for our robots ourselves.” He is responsible for all mechanical production at the institute with his six colleagues. This is a task that requires close cooperation with the design engineers at an early stage, as Dreer mentions: “Our components contain electronics and mechanics in the smallest of spaces. Every component must be designed to be manufactured sensibly – despite its complexity.” Each production specialist takes care of a component throughout the entire process chain, from ordering tools and materials to programming, machining, and quality assurance.”
Michael Dreer has been with DLR-RM for almost 30 years and has witnessed major robotic advances during this time: “In lightweight construction, there have always been steps in development that have placed increasing demands on our production technology.” In order to keep up, DLR-RM invested only a few years ago in several 5-axis machining centers, a turn-mill machine with driven tools, and a combined machining center that is equally capable of turning and milling. The simultaneous 5-axis machining, in particular, also made changing their CAD/CAM equipment necessary.
CAM system for state-of-the-art machining technology
Is our CAD software still up to date? What about the CAM module previously integrated into the CAD system? Will it meet future requirements? Those responsible asked these questions and concluded that the CAM programming should be independent of the design engineers’ CAD system. “Here in mechanical production, we need CAM software capable of exchanging data with all CAD systems and supporting us with simultaneous multi-axis machining and turn-mill centers. It also has to offer us high process reliability,” summarizes Michael Dreer.
When searching for such a future-proof CAM system, hyperMILL® from OPEN MIND soon became the focus of attention. “This software is very practical and offers powerful technologies. You can tell that it was developed by people with experience in machining and are familiar with the problems of complex components,” says Harald Wagner, Group Leader of Mechanical Production. “This is particularly evident in the easy-to-understand programming interface, even in the 5-axis area.”
The wide range of 5-axis functions that can be programmed quickly and easily was an important argument in favor of hyperMILL®. This is because the external structures of DLR robots have spherical 3D surfaces and have fixings and flanges in many orientations and undercuts, so that machining can often only be carried out on five axes. “With our previous system, it took a great deal of effort to master 5-axis programming. This meant that we only used five-axis milling when there was no other option,” reports Dreer.
That’s different now. Michael Dreer has been working with hyperMILL® for around three years and is the first in his department to do so. “It made sense, as I mainly work with complex 5-axis parts,” says the experienced precision mechanic. In the meantime, another colleague has switched to hyperMILL®. Others will gradually follow. According to Dreer, one of the strengths of hyperMILL® is its extensive, integrated tool database that allows centrally managing all tools for drilling, milling, and turning. It can be used to store spindle speed and feed rate values, individual values for materials, and even application cases. “It took a while for me to enter all the tool data, but now I save a lot of time when programming and selecting tools. I also benefit from optimal processes thanks to the reliable technology data,” says Dreer.
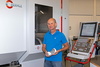
Michael Dreer, a precision mechanic at DLR-RM: “The investment in hyperMILL®, including VIRTUAL Machining and BEST FIT, has definitely paid off. We are faster at programming, we get an NC code simulation that gives us the greatest possible safety, and we can set up our printed components much more easily.”
Indispensable NC code simulation
Dreer is very enthusiastic about hyperMILL® VIRTUAL Machining (VM) that he added a year later: “This gives me a complete package from OPEN MIND that generates perfect NC codes and ensures almost one-hundred-percent collision-free machining thanks to precise NC code simulation.”
NC code simulation is nothing new in mechanical production at DLR-RM. Dreer and his colleagues consider it absolutely essential for five-axis machining: “The risk of a collision is simply too great. Even a well-established programmer with lots of experience can never predict with certainty what machine movements will actually look like. It’s not enough to simulate with pure CAM data.” This is why Dreer and his colleagues have been using separate simulation software for NC code simulation for some years now.
This was also initially used with hyperMILL®. Dreer sees this as a step forward: “Compared to our previous CAM software, hyperMILL® offers a better interface and easier data transfer. Everything is much faster now that we have the NC code simulation in the hyperMILL® VIRTUAL Machining Center. We have an end-to-end workflow, as hyperMILL® automatically makes all process-relevant data available. In no time at all, I get feedback on whether the program is running on the machine without collisions or not – with almost one-hundred-percent reliability.”
The support provided by hyperMILL® and the virtual machine is not only important to the production specialists at DLR-RM when it comes to five-axis milling. Programming the turn-mill center is also a demanding task that is supported by hyperMILL® TURN-MILL Machining. Michael Dreer adds: “To ensure maximum reliability here , we have made ourselves available as VM beta testers for turn-mill machining, which works extremely reliably.”
Automated job linking and BEST FIT
hyperMILL® VIRTUAL Machining also includes the Optimizer module in addition to NC code simulation. During NC code generation, this adapts the NC program perfectly to the kinematic properties of the machine automatically. The best positions are selected and optimized, linking movements are generated between individual operations. Michael Dreer uses the Optimizer primarily for job linking: “This function links my individual jobs with safe, optimized, and collision-free movements without me having to worry about it.”
While the DLR-RM production team saves programming time with the Optimizer, the BEST FIT function, available as an add-on for hyperMILL® VIRTUAL Machining, reduces the time to clamp and align the component. “In the past, we had a material removal volume of over 90 percent for our lightweight structures, which is why we now have these components manufactured using 3D metal printing or investment casting wherever possible,” explains Michael Dreer. “However, we also have to machine functional surfaces, drill holes, and threads on these parts.”
One difficulty was clamping the parts on the machine and aligning them precisely. This required complicated clamping devices and an enormous amount of time, as repeatability had to be achieved for subsequent parts. “With BEST FIT, we have found a way to set up parts quickly and machine them reliably,” says a delighted Harald Wagner.
BEST FIT is an intelligent component alignment function in the CAM system that allows the component to be fixed to the machine without being aligned. “We use inexpensive, printed plastic fixtures for this, for example,” says Michael Dreer, “as when clamping, it doesn’t come down to the millimeter.” The component is then measured on the machine with a 3D touch probe. The results are sent back to the CAM as a measuring log. hyperMILL® BEST FIT then moves the CAD component so that it is completely within the measured stock.
“I can check this on the screen, but it usually fits perfectly straight away.” BEST FIT then modifies the NC code accordingly, simulates it in relation to the actual clamping situation, and optimizes the program automatically. Michael Förster, Senior Product Marketing Manager at OPEN MIND, explains the next steps: “To ensure safe and accurate machining, the machine setter then performs a verification measurement. If the position on the machine matches the optimized program, machining can start without the machine setter having to laboriously align the component on the machine. The advantages include immense time savings, safe machining, and plannable processes.”
Michael Dreer and Harald Wagner agree wholeheartedly: “This saves us a lot of time and effort. The investment in hyperMILL® VIRTUAL Machining and BEST FIT has definitely paid off. We are faster at programming, we get an NC code simulation that gives us the greatest possible safety, and we can set up our printed components much more easily.”