Automated Programming – Quick and Easy
Häwitool AG | Amriswil, Switzerland
Tool and mold makers use hyperMILL® system to improve programming and milling performance: The Swiss tool and mold maker Häwitool relies on automation — in its machinery and now also in CAM programming. For this purpose, the company invested in the hyperMILL® CAM system from OPEN MIND, which makes a decisive contribution to fast, efficient programming and machining thanks to its advanced 5-axis strategies, the hyperMILL® MAXX Machining performance package, and the hyperMILL® AUTOMATION Center.
When Christoph Häberli and John Wirth’s founded their company in 2000, the idea was for Häwitool AG, to manufacture top-quality tool and mold making products. Their first company building was developed on a greenfield site in Amriswil, Switzerland, and it was equipped with state-of-the-art technology right from the start. “This is imperative to ensure we can use our precise injection mold tools successfully at our site,” says Christoph Häberli. “This is the only way to achieve short production times and a good price-performance ratio. We were convinced of this right from the beginning.”
The plan worked. In 2003, the two managing directors hired their first employee, Tobias Roffler, who is now the milling team leader. By 2011, there were ten employees, and today there are over 26 employees. Häwitool successively invested in the expansion of its machinery and innovative software, with the first 5-axis machining center installed in the production hall in 2007. This was soon followed by a DMG MORI HSC 105 5-axis machine equipped with linear drives for finishing large components and a smaller DMG MORI HSC 55 with a Workmaster system from System 3R for fully automated electrode milling.
“With the hyperMILL AUTOMATION Center, we’ve cut recurring task times by 50 percent.”
Tobias Roffler, Milling Team Leader
Strong in electrode production as well as die-sinking and wire EDM
Other machine highlights include the two GF AgieCharmilles Form X600 EDM cells with 180 electrodes and 13 pallets. “Our mold-making has taken a major step forward thanks to these automated machines, and they’ve led to numerous EDM orders from other industrial sectors,” says Christoph Häberli. “The same applies to the AgieCharmilles CUT P 550 wire EDM machine that we purchased at the beginning of 2023.”
These investments illustrate the importance of innovation and automation at Häwitool. However, the right digital structures also need to be in place. The tool and mold makers, therefore, reorganized in 2016 – with an ERP system that takes over the complete work planning for each individual tool component and an MES system which, according to Häberli, is extremely helpful for work processes and costing: “Every employee is involved and benefits from the visualized production orders and capacities. We have also ensured data consistency, from incoming orders, CAD and CAM to quality assurance, supporting largely paperless production.”
New CAM system speeds up processes
An important feature of Häwitool’s corporate strategy is never to sit back and take it easy, but to seek opportunities for optimization continuously. In 2021, the managers agreed that CAM programming had become a bottleneck that urgently needed to be eliminated. “The parts we produce are increasingly complex in terms of geometry and much more demanding when it comes to the milling paths. Although we were able to program every component with our previous CAM software, the effort involved was sometimes enormous,” explains Christoph Häberli. “The machining times with the milling strategies available also offered considerable potential for improvement.”
To exploit the opportunity and automate programming, the mold makers invested in the hyperMILL® CAD/CAM system from OPEN MIND Technologies AG. Contact with the CAM specialists based in Wessling, Germany, had already existed for some time. “Friends of the company had repeatedly reported on the ease of use, the automation options, and the very efficient 5-axis programming options in hyperMILL®,” mentions Häberli. “We were also very impressed by the simultaneous five axis milling results.” The only point of caution was the changeover phase, as the company did not want to interrupt production operations for too long.
Easy system change
The fears turned out to be unfounded and the switch to hyperMILL® took place at the beginning of 2022 without any major issues. Tobias Roffler, the milling team leader and most experienced CAM programmer, played a key role in this. In close consultation with Sinisa Stankovic, OPEN MIND Sales Manager for Switzerland, he developed a plan where he was initially trained as the key user with team members following afterwards. Roffler then helped and advised them. Sinisa Stankovic explains: “We offer comprehensive training consisting of basic courses on hyperMILL® as well as various advanced courses. For the Häwitool team, we conducted the basic training sessions in person. The training sessions on feature and macro technology, 5-axis technology, the tool database, and the hyperMILL® AUTOMATION Center were carried out with a customized mix of in-person and online training.”
Machining time reduced from three hours to 30 minutes
Now, a total of nine employees have been trained to program parts with hyperMILL® and machine them on the milling machines. “In a very short time they familiarized themselves with hyperMILL® and were able to quickly create sophisticated NC programs for 5-axis machining. We were also impressed by the automation options, as they save us a lot of routine work and give us more time for the really interesting tasks,” says Tobias Roffler. “This includes the hyperMILL® MAXX Machining performance package. It’s really fun to see how much faster we can finish and rough with it. We’re also increasingly using 5-axis simultaneous milling for both electrodes and molded parts. We could never really get to grips with this in our previous system but hyperMILL® makes programming really easy, and the right strategies are always available. We achieve far better surfaces with a milling pattern that is more even. This wasn’t possible before.”
Tobias Roffler uses a few components to illustrate the savings that can be made, such as the lateral slider for an injection-molded plastic part. The vertical planes were machined using a barrel cutter and the “tangent plane machining” strategy from the hyperMILL® MAXX Machining package. “The process used to take three hours and 40 minutes. Now machining only takes 30 minutes,” says Roffler. Referring to mold core in which the mold separation was also milled tangentially with a conical barrel cutter, the team achieved a time saving of a factor of eight.
CAM programming is increasingly automated
Automation technology was another decisive reason for choosing hyperMILL®. It helps to standardize the programming of similar geometries, recurring shape elements, and features such as holes or pockets. This saves the user time and reduces the risk of errors.
An important part of the automation technology in hyperMILL® is the advanced feature and macro technology. It allows geometry information from the CAD model to be used automatically for CAM programming. Sinisa Stankovic explains: “This is not limited to standard features such as holes and pockets, but applies to almost all geometry information, which is combined using colors, shapes or layer names. This can then be automatically transferred to the NC program using the manufacturing expertise stored in macros.”
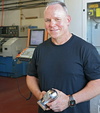
Christoph Häberli, Managing Director of Häwitool: “We are all delighted with our new hyperMILL® CAD/CAM software. The system is easy to use and provides excellent milling strategies that save us a lot of time. I appreciate the automation options offered by the hyperMILL® AUTOMATION Center that we will continue to expand in the future.”
Tool database also stores technology data
A well-maintained tool database provides an important basis for automated CAM programming. The solution provided by hyperMILL® makes it possible to manage all types of tools – from drills and milling cutters to complex turning tools. They can be mapped virtually and linked with technology data.
For Tobias Roffler and his team, the system changeover provided a welcome opportunity to rebuild the tool database: “We have tried to standardize our tools as much as possible to minimize the inventory. We have stored extensive data for each tool, including materials and applications. This allows us to easily select the right tool and cutting values for each machining operation. This database is just as essential for automated programming as our well-trained employees.”
hyperMILL® AUTOMATION Center: 50 percent time savings
Häwitool also purchased a license for the hyperMILL® AUTOMATION Center Advanced to make optimum use of all CAM automation options. Sinisa Stankovic explains: “The hyperMILL® AUTOMATION Center Advanced offers a level of technology that reaches far beyond the automation of standard geometry features. The specific characteristics of the CAD models are only of secondary importance in this context. The main focus is on the elements that a CAD model can contain. hyperMILL® users can define and standardize complex processes and specify the process steps using a wide range of template functions.”
At Häwitool, three employees will initially be working with the hyperMILL® AUTOMATION Center. One of them is Felix Gasser. According to his experience: “Once you’ve got to grips with the software and its many possibilities, you can achieve great success.” He and his colleagues initially concentrated on electrode production and they automated recurring tasks such as creating jobs, defining planes, setting origins, coloring, labeling, and more. “This doesn’t mean that programmers are completely left out. Instead, the AUTOMATION Center guides them interactively through the individual process steps. The programmer specifies whether it’s a copper or graphite electrode to be machined, and they can also intervene to correct other suggested details,” explains Felix Gasser.
Is it a success? “Compared to before, we’ve cut recurring task times by 50 percent,” confirms team leader Roffler. “Of course, this motivates us to utilize the automation options even more intensively in the future.”