Su simulación de código CN con toda la información de CAM importante
hyperMILL® VIRTUAL Machining Center
hyperMILL® VIRTUAL Machining Center le permite simular y analizar previamente el proceso de producción para minimizar así las operaciones ineficientes y los errores costosos.
hyperMILL® VIRTUAL Machining Center combina las ventajas de una simulación basada en datos de CAM con las de una simulación de código CN. El resultado es una simulación de código CN con toda la información necesaria para el proceso desde el sistema de CAM hyperMILL®, como sobreespesores negativos, aristas rotas o parámetros de agujeros. Solo así evitará que en estos mecanizados se detecte erróneamente una colisión, y se ahorrará tener que realizar una interminable evaluación de estas áreas de colisión.
Nuestro VIRTUAL Machining Center le ofrece todas las opciones clásicas de simulación integradas en una interfaz de usuario muy intuitiva. La simulación de la máquina se lleva a cabo en un gemelo digital de la máquina real y tiene en cuenta, además de la pieza de trabajo, la pieza en bruto y la herramienta, también la sujeción, el utillaje y los sistemas de fijación. Por tanto, nuestra simulación de máquina basada en código NC garantiza una detección de colisiones fiable y los procesos de posicionamiento son mucho más eficaces y seguros.
Características
- Basado en código NC
- Gemelo digital de la máquina
- Comprobación visual independiente del control de colisiones
- Simulación de todas las trayectorias de herramientas y de unión
- Control de final de carrera
- Simulación de retirada de material
- Numerosas funciones de análisis
- Comprobación de máquina, sujeción, herramienta, modelo y pieza en bruto
- Prueba de fijaciones
Información de proceso desde el sistema CAM
Los sistemas de simulación convencionales simulan el mecanizado con ayuda de datos de trayectorias de herramienta internos del sistema CAM o bien basándose en el código CN creado. Sin embargo, para que sus programas de CN puedan simular de forma realmente segura e inequívoca, además del código CN también se debe evaluar la información relevante para el proceso procedente del sistema CAM. Y eso es exactamente lo que hace hyperMILL®, pues la simulación propia del código CN proporciona, además del código CN, toda la información de fabricación necesaria. Un ejemplo: usted programa tareas de mecanizado en hyperMILL® y asigna sobreespesores negativos o procesa detalles no modelados como biseles. Normalmente, estas transgresiones diseñadas intencionadamente en las piezas se interpretan como colisiones y usted debe evaluarlos a posteriori. Pero no es así con hyperMILL® VIRTUAL Machining Center: simula y comprueba todos los mecanizados de forma inequívoca para garantizar la máxima seguridad.
De este modo, se tienen en cuenta, por ejemplo, las siguientes informaciones del proceso:
- Sobreespesores negativos
- Áreas de recorte
- Detalles no modelados
- Desbarbado automático: rotura de chaflanes y esquinas
- Escribiendo
«hyperMILL® VIRTUAL Machining Center es la clave para conformar procesos de posicionamiento de modo más eficiente y seguro».
Dr. Josef Koch
Director de desarrollo de OPEN MIND Technologies AG
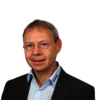
Análisis a fondo del programa de CN
Además de sus eficaces simulaciones, hyperMILL® VIRTUAL Machining Center ofrece numerosas funciones de análisis. Eso significa que usted puede comprobar de forma detallada cualquier situación de mecanizado. Los distintos diagramas de ejes permiten obtener conclusiones sobre la calidad del proceso de mecanizado. Todos los movimientos de desplazamiento de los distintos ejes, así como los avances y la velocidad del eje son visibles en todo momento para el programador de CNC, lo cual le permite evitar errores y operaciones poco eficientes.
Funciones de análisis en hyperMILL® VIRTUAL Machining Center
Control del área de trabajo
Con ayuda de un modelo de la máquina almacenado se puede controlar si las trayectorias sobrepasan algún final de carrera en los mecanizados simultáneos 2,5D, 3D, 3+2 y de 5 ejes. En esta comprobación se consideran tanto los ejes lineales X, Y y Z como los circulares A, B y C, además de los sistemas y utillajes de fijación.
Establecimiento de puntos de parada
Para comprobar de manera fiable los puntos críticos y valorar con mayor exactitud los procesos sucesivos, la simulación se debe detener en puntos concretos. En determinadas condiciones, por ejemplo, al cambiar una herramienta o al cambiar de un movimiento de avance G1 a uno G0, se pueden generar paradas automáticamente. Además, las paradas también se pueden crear manualmente mediante eventos NC o con un punto arbitrario en la trayectoria de la herramienta.
Diagramas de ejes
Saltar a los puntos de simulación
Es posible saltar hacia delante o hacia atrás a puntos específicos del código NC en cualquier momento. La pieza en bruto se actualiza automáticamente para el punto de simulación seleccionado. Los puntos se pueden seleccionar mediante puntos de parada automáticos, a través de la gestión del programa, tomando las trayectorias de las herramientas o eligiendo cualquier punto del código NC.