Votre simulation de code CN avec toutes les informations FAO importantes
hyperMILL® VIRTUAL Machining Center
hyperMILL® VIRTUAL Machining Center vous permet de simuler et d’analyser le processus de fabrication à l’avance, ce qui réduit les opérations inefficaces et les erreurs coûteuses.
hyperMILL® VIRTUAL Machining Center combine les avantages d’une simulation basée sur des données FAO avec ceux d’une simulation de code CN. Le résultat est une simulation de code CN avec toutes les informations de processus nécessaires provenant du système FAO hyperMILL®, telles que les surépaisseurs négatives, les bords cassés ou les paramètres de perçage. C’est le seul moyen d’éviter de détecter à tort une collision pendant ces opérations d’usinage et de s’épargner une évaluation fastidieuse de ces zones de collision.
Notre VIRTUAL Machining Center vous offre toutes les possibilités classiques de simulation, intégrées dans une interface utilisateur très intuitive. La simulation machine s’effectue sur un jumeau numérique de la machine réelle et tient compte non seulement de la pièce, du brut et de l’outil, mais aussi des porte-outils, des gabarits et des moyens de serrage. Ainsi, notre simulation machine basée sur le code CN garantit une détection fiable des collisions, et les processus de rodage sont nettement plus efficaces et plus sûrs.
Caractéristiques
- Sur la base du code CN
- Jumeau numérique de la machine
- Contrôle visuel indépendant du contrôle de collision
- Simulation de tous les trajets d’outils et des liaisons
- Contrôle des interrupteurs de fin de course
- Simulation avec enlèvement de matière
- Fonctions d’analyse étendues
- Inspection de la machine, du porte-outils, de l’outil, du modèle et du modèle brut
- Test des bridages
Informations de processus provenant du système FAO
Les systèmes de simulation standard simulent l’usinage soit à l’aide des données de trajets d’outils internes du système FAO, soit sur la base du code CN créé. Toutefois, pour que vous puissiez simuler vos programmes CN de manière vraiment fiable et sans ambiguïté, les informations de processus pertinentes du système FAO doivent également être évaluées en plus du code CN. C’est exactement ce que hyperMILL® peut faire, car il fournit sa propre simulation de code CN avec toutes les informations de fabrication nécessaires en plus du code CN. Exemple : vous programmez des opérations d’usinage pertinentes dans hyperMILL® et vous attribuez des surépaisseurs négatives ou vous usinez des détails non modélisés tels que des chanfreins. Normalement, ces violations intentionnelles de composants sont détectées comme des collisions et vous devrez les analyser ultérieurement. Ce n’est pas le cas avec hyperMILL® VIRTUAL Machining Center: il simule et contrôle parfaitement toutes les opérations d’usinage, pour une sécurité maximale.
Par exemple, les informations de processus suivantes sont alors prises en compte:
- Surépaisseurs négatives
- Zones de coupe
- Détails non modélisés
- Ébarbage automatique : casser les chanfreins et les angles
- Écriture
« hyperMILL® VIRTUAL Machining Center est la clé pour programmer les processus d’engagement de façon nettement plus sûre et performante. »
Dr. Josef Koch,
Directeur technique, OPEN MIND Technologies AG
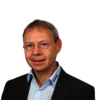
Analyse approfondie du programme CN
Outre une simulation efficace, hyperMILL® VIRTUAL Machining Center offre des fonctions d’analyse étendues. Cela signifie que vous pouvez vérifier chaque situation d’usinage en détail. Plusieurs diagrammes d’axes permettent de tirer des conclusions quant à la qualité du fonctionnement de la machine. Tous les mouvements d’avance des différents axes, les avances et la vitesse de la broche sont visibles à tout moment par le programmeur CNC, qui peut alors éviter les erreurs et les opérations inefficaces.
Fonctions d’analyse dans hyperMILL® VIRTUAL Machining Center
Surveillance de l’espace de travail
Le dépassement éventuel des limites de butée lors des usinages en 2,5 axes, 3 axes, 3+2 et 5 axes continus est contrôlé à l’aide d’un modèle de machine enregistré. Les axes linéaires X, Y, Z ainsi que les axes rotatifs A, B, C sont vérifiés. Les dispositifs de serrage et les gabarits sont pris en compte.
Définition des points d’arrêt
Afin de contrôler les points critiques en toute sécurité et d’évaluer plus précisément la procédure à suivre, la simulation peut s’arrêter à des points précis. Dans certaines conditions, par exemple en cas de changement d’outil ou lors du passage d’un mouvement d’avance G1 à G0, des points d’arrêt peuvent être créés automatiquement. En outre, il est possible de sélectionner manuellement les points d’arrêt via une ligne de bloc CN ou de les saisir via un point quelconque sur le trajet d’outil.
Diagrammes d’axes
Sauts vers des postes de simulation
Il est possible à tout moment d’effectuer des sauts avant/arrière vers certains endroits du code CN. Le modèle brut est automatiquement mis à jour pour le point de simulation sélectionné. Les points peuvent être sélectionnés soit par des points d’arrêt automatiques, soit par la gestion du programme, soit par prélèvement sur les trajets d’outils, soit à n’importe quel endroit du code CN.