Programmazione più rapida, fresatura più veloce
ANDREAS STIHL AG & Co. KG | Waiblingen, Germania
Con hyperMILL® e la funzione BEST FIT, STIHL accelera la prototipizzazione
Da due anni, il reparto di produzione CNC nello stabilimento dei pezzi di prova di STIHL utilizza il sistema CAD/CAM hyperMILL® di OPEN MIND. Il risultato: una maggiore efficienza. A questo contribuisce, oltre alla rapida programmazione dei centri di lavoro a 5 assi, il modulo hyperMILL® VIRTUAL Machining con la funzione BEST FIT: l’orientamento dei componenti diventa un “gioco da ragazzi”, garantendo un processo di fresatura preciso.
Motosega - STIHL. Non c’è boscaiolo che non conosca questi attrezzi dal caratteristico colore arancione. L’azienda familiare di Waiblingen è leader mondiale nel settore delle motoseghe dal 1971, ma ha molto altro da offrire: numerose attrezzature per segare e tagliare, falciare e piantare, pulire e riordinare.
Motosega - STIHL. Non c’è boscaiolo che non conosca questi attrezzi dal caratteristico colore arancione. L’azienda familiare di Waiblingen è leader mondiale nel settore delle motoseghe dal 1971, ma ha molto altro da offrire: numerose attrezzature per segare e tagliare, falciare e piantare, pulire e riordinare.
La motivazione dell’azienda è, come si legge sulla homepage, “facilitare il lavoro dell’uomo nella natura”. Viene coltivata una forte cultura dell’innovazione al fine di creare valore aggiunto per i clienti con nuove tecnologie. Il centro di ricerca e sviluppo presso la sede centrale di Waiblingen, dove più di 700 sviluppatori lavorano insieme per tutti i reparti, è altrettanto importante.
Qui si trova anche il servizio pezzi di prova nell’area di convalida del sistema, che collabora con gli sviluppatori e i progettisti. Nel gruppo “Produzione additiva e CNC” vengono prodotti prototipi, piccole serie e campioni iniziali. Il capogruppo Boris Matuschka descrive il campo di attività: “Produciamo le parti e i componenti creati virtualmente dalla progettazione e dallo sviluppo in alluminio, magnesio, acciaio, ottone e plastica. Vengono utilizzati per testare i nostri nuovi prodotti. Per il nostro team, questo significa che dobbiamo essere molto flessibili e reattivi per ridurre al massimo il time to market”.
Se possibile, i componenti vengono prodotti mediante truciolatura. Per la fresatura sono disponibili attrezzature all’avanguardia, tra cui due centri di lavoro simultanei a 5 assi e tre fresatrici a 3+2 assi. “Per i componenti difficili da produrre con la fresatura, utilizziamo tra l’altro un impianto di fusione a getto per la produzione additiva che può lavorare varie polveri metalliche”, spiega Boris Matuschka. “Questi pezzi prodotti in modo additivo richiedono solitamente una ripresa di truciolatura per garantire le dimensioni funzionali e le finiture superficiali richieste”.
“L’investimento in hyperMILL® ha dato i suoi frutti. L’efficienza della programmazione è aumentata e siamo stati in grado di sfruttare la macchina in modo significativamente maggiore. Stiamo quindi cercando di estendere l’uso di questo software ad altre macchine”.
Matuschka riassume così
Eliminare l‘ostacolo della programmazione NC
La lavorazione a 5 assi per piccole serie e la prototipizzazione rappresenta una tecnologia ideale, in quanto di solito può portare a un componente finito con un unico staffaggio. Il prerequisito fondamentale è un programma NC implementabile e che garantisca la sicurezza dei processi. “Questo ha rappresentato un ostacolo per noi in passato”, afferma il capogruppo Matuschka. “La programmazione con il sistema precedente richiedeva più tempo e, in caso di eccesso di capacità, era necessario ricorrere in via aggiuntiva a fornitori di servizi esterni”.
La soluzione offerta da STIHL è stata la seguente: “Trasferiamo la capacità in eccesso a fornitori di servizi esterni oppure garantiamo una maggiore efficienza e quindi una maggiore produzione di pezzi nel nostro stabilimento grazie a un nuovo sistema CAM”. Si è optato per un nuovo sistema e il team responsabile ha cercato la soluzione CAD/CAM ottimale. Quattro sistemi sono stati ammessi alla preselezione, due dei quali alla fase di test approfondito. “Abbiamo concordato con i fornitori un testing in cui abbiamo potuto conoscere i due sistemi in condizioni reali e metterli alla prova con i nostri pezzi”, racconta Boris Matuschka. “Durante questo periodo, abbiamo anche avuto la nostra prima esperienza con l’assistenza dei rispettivi fornitori”.
In questo caso, il futuro partner di riferimento, OPEN MIND Technologies AG, Wessling, ha subito potuto raccogliere punti a favore, come spiega Benjamin Gruber, tecnico e programmatore, con l’aiuto di un esempio: “Il sistema CAM hyperMILL® offre una funzione di ‘indicizzazione automatica’ estremamente innovativa per la lavorazione a 5 assi. Questa consente di programmare e fresare in un’unica operazione aree la cui lavorazione richiede più inclinazioni dell’utensile. Volevamo utilizzare questa funzione anche per le macchine a 3+2 assi. OPEN MIND ha soddisfatto la nostra richiesta e ha sviluppato una soluzione adeguata”.
hyperMILL®, un benchmark di successo
La decisione finale a favore di hyperMILL® è stata presa sulla base dell’esperienza acquisita nella fase di test e di un benchmark con un pezzo di riferimento impegnativo. Per questo, STIHL ha chiesto ai due fornitori CAM di mettere a disposizione un programmatore specializzato nei rispettivi software che si sarebbe occupato della programmazione CAM. “Volevamo un confronto neutrale di ciò che si può sfruttare al massimo dai due programmi CAM, indipendentemente da ciò che abbiamo imparato finora”, spiega Benjamin Gruber.
Steffen Völker, Technical Key Account Manager e specialista applicativo per la costruzione di stampi e prototipi, ha preso in carico questo compito per OPEN MIND. Si trattava di fresare un componente del basamento che contiene molte aree che devono essere inclinate o fresate contemporaneamente. Un’altra difficoltà era rappresentata dalle nervature strette, che devono essere lavorate con utensili di piccole dimensioni. Con hyperMILL® Steffen Völker ha ridotto i tempi di programmazione e di lavorazione della macchina, tanto che STIHL ha deciso alla fine di optare per hyperMILL®.
Benjamin Gruber elogia l’intuitività del sistema. Dopo due settimane di formazione base, aveva già acquisito una familiarità tale con il software che la programmazione di pezzi a 5 assi non rappresentava più un problema: “hyperMILL® offre un’ampia scelta di funzioni a 5 assi che possono essere programmate con un’ampia automatizzazione. Il processo risulta rapido ed è un grande punto di forza di questo sistema CAM”.
Una soluzione completa, dal CAD alla macchina
Cita il pacchetto completo OPEN MIND come ulteriore vantaggio decisivo. Finora nello stabilimento di pezzi di prova di STIHL erano necessarie diverse soluzioni software per soddisfare i requisiti della lavorazione moderna. “In passato, avevamo costruito un intero ecosistema attorno al sistema di programmazione, con un sistema di simulazione aggiuntivo, un database di utensili e così via”, aggiunge il tecnico. “Abbiamo dovuto utilizzare diversi sistemi per arrivare dove volevamo. hyperMILL® ora offre tutto in uno”.
All’interno del software CAD/CAM hyperMILL®, è soprattutto il modulo VIRTUAL Machining a fare la differenza rispetto agli altri sistemi. In un certo senso, è la pietra miliare per la generazione del codice NC e la simulazione del codice NC, nonché per varie funzioni. Lo specialista applicativo OPEN MIND Steffen Völker spiega: “Poiché sviluppiamo il nostro software in autonomia, siamo stati in grado di garantire una soluzione valida e completa. Questo include anche una precisa simulazione del codice NC, che ha a disposizione tutti i dati rilevanti per il processo di hyperMILL® e garantisce la massima sicurezza dei processi”.
L’orientamento intelligente dei componenti
Völker sottolinea la funzione BEST FIT, disponibile come add-on per hyperMILL® VIRTUAL Machining: “La semplicità di orientamento dei componenti prodotti in modo additivo è particolarmente importante per STIHL. Con hyperMILL® BEST FIT, offriamo una funzione innovativa che riduce in modo significativo il dispendio di tempo e quindi l’orientamento dei componenti sulla macchina”.
Benjamin Gruber descrive qual era lo standard precedente: “Abbiamo adeguato il componente e lo staffaggio della macchina alle condizioni del programma NC. Ciò significa che abbiamo orientato il componente manualmente con il comparatore. Questo processo doveva essere ripetuto fino a quando l’orientamento veniva registrato con la massima precisione possibile”.
Con hyperMILL® BEST FIT, l’orientamento in tempo reale avviene direttamente tramite il software CAM. “Eseguiamo una misurazione 3D dal componente non orientato sulla macchina e riproduciamo i punti di misura nel sistema CAM”, spiega Benjamin Gruber. “Tutto il resto lo fa il software”. Adatta il codice NC alla posizione misurata del componente e sposta virtualmente i percorsi utensile rispetto al componente. Il codice NC adattato viene sottoposto a simulazione nella macchina virtuale, per essere poi automaticamente ottimizzato. Per garantire una lavorazione sicura e precisa, il configuratore della macchina interviene nuovamente: esegue una misurazione di verifica che controlla nel sistema CAM se l’orientamento rientra nella tolleranza predefinita. Successivamente, è possibile avviare la lavorazione.
Lo specialista di fresatura e programmazione Gruber conferma: “Per noi questo significa un enorme guadagno di tempo. Inoltre, grazie alla misurazione di verifica, possiamo essere certi che la lavorazione avvenga senza collisioni e che alla fine si ottenga il risultato di fresatura desiderato”.
Ideale per la finitura di componenti stampati in 3D
BEST FIT è particolarmente utile per i componenti prodotti in modo additivo. Per un’ulteriore lavorazione, questi vengono solitamente sottoposti a finitura, il che avviene sulla macchina a 5 assi. A causa delle complesse geometrie dei componenti con molte superfici a forma libera, l’analisi sulla macchina è spesso difficile. In passato sono state introdotte in modo costruttivo caratteristiche specifiche che potevano essere analizzate. “Ora possiamo semplicemente serrare il componente stampato nella macchina, avviare il processo di misurazione e lasciare che la finitura proceda senza rischi”, spiega Benjamin Gruber.
“Un altro punto di forza di hyperMILL®, di grande importanza per l’efficienza nella produzione di pezzi, è rappresentato dalla possibilità di convertire facilmente i programmi a 5 assi in programmi a 3+2 assi. Ciò significa che, se necessario, i programmi possono essere trasferiti dalle macchine a 5 assi a quelle a 3+2 assi, evitando così i fermi”, sottolinea Boris Matuschka.
Galleria
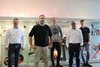
Il successo del lavoro di squadra: (da sinistra a destra) Aleš Vurušič, Key Account Manager di OPEN MIND, Boris Matuschka, Capogruppo produzione additiva e CNC dello stabilimento pezzi di prova di STIHL, Benjamin Gruber, Tecnico di STIHL, Steffen Völker, Technical Key Account Manager di OPEN MIND e Manfred Guggemos, Product Manager di OPEN MIND