Snel geprogrammeerd en betrouwbaar 5-assig bewerkt
Institute of Robotics and Mechatronics (DLR-RM) | Oberpfaffenhofen, Duitsland
Simultane 5-assige bewerking – alleen als het niet anders kan. Dat was jarenlang het motto in de mechanische productie aan het Instituut voor Robotica en Mechatronica in het Duitse Lucht- en Ruimtevaartcentrum (DLR). Na de introductie van de CAD/CAM-software hyperMILL van OPEN MIND, inclusief de simulatietechnologie VIRTUAL Machining en de functie BEST FIT, is dit echter veranderd. De verspaningsspecialisten kunnen nu in korte tijd geoptimaliseerde 5-assige NC-programma's genereren, die na de simulatie van de NC-code betrouwbaar zijn gecontroleerd op botsingen. Dankzij BEST FIT kunnen ook 3D-geprinte componenten snel en eenvoudig worden opgespannen en nauwkeurig worden bewerkt.
De DLR-vestiging in Oberpfaffenhofen bij München biedt onder andere onderdak aan het Instituut voor Robotica en Mechatronica, kortweg DLR-RM. Hier werken onderzoeksteams en studenten samen aan robotarmen, -handen en -grijpers. Ze ontwikkelen meerarmige systemen en mobiele platforms om andere planeten, kometen en asteroïden te verkennen, bodemmonsters te nemen, enzovoort. Bijzonder indrukwekkend zijn de grotendeels autonome vlieg- en looprobots en de humanoïde robots. Een voorbeeld hiervan is TORO, de humanoïde looprobot. Met TORO onderzoeken de wetenschappers de mogelijkheden op het gebied van tweebenige, dynamische voortbeweging: Momenteel leert TORO stabiel te lopen, trappen op te gaan, en nog veel meer.
"De investering in hyperMILL, inclusief de simulatietool VIRTUAL Machining en BEST FIT, heeft absoluut zijn vruchten afgeworpen. We kunnen nu sneller programmeren, we beschikken over een NC-codesimulatie die ons maximale zekerheid biedt en we kunnen onze geprinte componenten veel eenvoudiger instellen."
Michael Dreer, fijnmechanicus bij DLR-RM
De robots worden hier niet alleen ontwikkeld, maar ook gebouwd
Michael Dreer is fijnmechanicus bij DLR-RM. Hij legt uit dat de hier ontwikkelde robotsystemen niet alleen worden gebruikt in de lucht- en ruimtevaartindustrie, maar ook in de medische technologie, service, zorg en de moderne industrie. "We doen hier fundamenteel onderzoek, maar dan wel op basis van specifieke projecten. Vaak met partners uit de industrie, maar ook op eigen initiatief," vertelt Dreer, die erop wijst dat DLR-RM naast robot kinematica ook systeemcomponenten ontwikkelt, zoals bijzonder kleine en lichte motoren, beeldverwerkingssystemen, besturingseenheden en een breed scala aan software.
"Maar we houden ons niet alleen bezig met het ontwikkelen daarvan," benadrukt Dreer. "We hebben hier een zeer hoge mate van verticale integratie en produceren alle geavanceerde onderdelen voor onze robots zelf." Samen met zijn zes collega's is hij verantwoordelijk voor alle mechanische productie binnen het instituut. Deze taak vereist al in een vroeg stadium nauwe samenwerking met de ontwerpers, aldus Dreer: "Onze componenten bevatten elektronica en mechanica in een uiterst krappe ruimte. Elk onderdeel moet zo worden ontworpen dat het, ondanks de complexiteit ervan, ook op een redelijke manier kan worden vervaardigd." Elk van de productiespecialisten is persoonlijk verantwoordelijk voor het begeleiden van een component in de volledige procesketen, van het bestellen van gereedschappen en materialen tot het programmeren, machinaal bewerken en de kwaliteitsborging.
Michael Dreer werkt al bijna 30 jaar bij DLR-RM en heeft in die tijd een grote vooruitgang in de robottechnologie waargenomen: "Vooral op het gebied van lichtgewicht constructies zijn telkens opnieuw ontwikkelingsstappen gezet die steeds hogere eisen stelden aan onze productietechnologie." Om bij te blijven, investeerde DLR-RM enkele jaren geleden in meerdere 5-assige bewerkingscentra, een draaifreesmachine met aangedreven gereedschappen en een gecombineerd bewerkingscentrum dat voor zowel draaien als frezen geschikt is. Ook in de CAD/CAM-apparatuur waren aanpassingen nodig, vooral vanwege de simultane 5-assige bewerkingen.
CAM-systeem voor ultramoderne verspaningstechnologie
Is onze CAD-software nog up-to-date? Hoe staat het met de CAM-module die momenteel is geïntegreerd in het CAD-systeem? Beantwoordt die module nog aan de toekomstige eisen? De verantwoordelijke medewerkers stelden zich deze vragen en kwamen tot de conclusie dat de CAM-programmering onafhankelijk moest zijn van de fabrikanten van het CAD-systeem. "In onze mechanische productie hebben we CAM-software nodig die gegevens kan uitwisselen met alle CAD-systemen en zowel meerassige simultane bewerkingen als draaifreescentra ondersteunt. Daarnaast moet de software ons een hoge mate van procesbetrouwbaarheid bieden", vat Michael Dreer samen.
Tijdens de zoektocht naar een dergelijk toekomstbestendig CAM-systeem kwam al snel hyperMILL van OPEN MIND in beeld. "Deze software is uiterst praktijkgericht en biedt krachtige technologieën. Je merkt dat de programma's zijn ontwikkeld door mensen die zelf ervaring hebben met machinale bewerkingen en bekend zijn met de problemen van complexe componenten", verklaart Harald Wagner, groepsmanager Mechanische Productie. "Dat komt vooral tot uiting in de makkelijk te begrijpen programmeerinterface, zelfs als het gaat om 5-assige toepassingen."
Het brede aanbod aan snel en eenvoudig te programmeren 5-assige features was een belangrijk argument om voor hyperMILL te kiezen. Immers, de externe structuren van DLR-robots bevatten bolvormige 3D-oppervlakken, bevestigingspunten en flenzen in tal van richtingen, plus ondersnijdingen, wat betekent dat bewerkingen vaak alleen 5-assig kunnen worden uitgevoerd. "Met ons vorige systeem kon het 5-assig programmeren alleen met veel moeite worden gerealiseerd. Daarom gebruikten we het 5-assig frezen alleen als het echt niet anders kon", meldt Dreer.
Maar dat is nu veranderd. Michael Dreer werkt inmiddels ongeveer drie jaar met hyperMILL en was daarmee de eerste op zijn afdeling. "Dat was een voor de hand liggende keuze, aangezien ik voornamelijk werk met complexe 5-assige componenten", vertelt de ervaren fijnmechanicus. Een collega van hem is ook overgestapt op hyperMILL en de anderen zullen geleidelijk volgen. Dreer beschouwt de uitgebreide, geïntegreerde gereedschapsbibliotheek, waarin alle gereedschappen voor boren, frezen en draaien centraal kunnen worden beheerd, als een van de sterke punten van hyperMILL. Deze bibliotheek kan worden gebruikt om toerental- en voedingswaarden, afzonderlijke technologische waarden voor materialen en zelfs toepassingen op te slaan. "Het duurde wel even om alle gereedschapsgegevens in te voeren. Maar nu bespaar ik veel tijd bij het programmeren en selecteren van gereedschappen. Daarnaast profiteer ik van geoptimaliseerde processen dankzij betrouwbare technologiegegevens", licht Dreer toe.

Michael Dreer, fijnmechanicus bij DLR-RM: "De CAD/CAM-software hyperMILL van OPEN MIND is uiterst praktijkgericht en biedt krachtige technologieën. Je merkt dat de programma's zijn ontwikkeld door mensen die zelf ervaring hebben met machinale bewerkingen en bekend zijn met de problemen van complexe componenten."
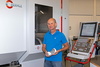
Michael Dreer, fijnmechanicus bij DLR-RM: "De investering in hyperMILL, inclusief de simulatietool VIRTUAL Machining en BEST FIT, heeft absoluut vruchten afgeworpen. We kunnen nu sneller programmeren, we beschikken over een NC-codesimulatie die ons maximale zekerheid biedt en we kunnen onze geprinte componenten veel eenvoudiger instellen."
Onmisbaar: simulatie van de NC-code
Dreer is bijzonder enthousiast over hyperMILL VIRTUAL Machining (VM), dat hij een jaar later toevoegde: "Daarmee beschik ik over een totaalpakket van OPEN MIND dat perfecte NC-codes genereert en via nauwkeurige simulatie van de NC-code ook met bijna honderd procent zekerheid garandeert dat er geen botsingen zullen optreden."
Simulatie van de NC-code is echter geen nieuw fenomeen in de mechanische productie bij DLR-RM. Dreer en zijn collega's beschouwen dit als absoluut noodzakelijk voor 5-assige bewerkingen: "Het risico dat door een botsing ernstige schade ontstaat, is gewoonweg te groot. Zelfs een ervaren, in de praktijk geschoolde programmeur kan nooit precies voorspellen hoe de bewegingen op de machine daadwerkelijk zullen verlopen. Als je op basis van alleen de CAM-gegevens simuleert, geeft dat niet voldoende zekerheid." Daarom gebruiken Dreer en zijn collega's al jaren gescheiden simulatiesoftware voor het simuleren van NC-codes.
Aanvankelijk werd deze software ook gebruikt in combinatie met hyperMILL. Een stap vooruit voor Dreer: "Vergeleken met onze vorige CAM-software biedt hyperMILL een betere interface en vereenvoudigde gegevensoverdracht. Maar sinds we over de NC-codesimulatie van het hyperMILL VIRTUAL Machining Center beschikken, gaat alles nog veel sneller. Doordat hyperMILL automatisch alle procesrelevante gegevens aanlevert, hebben we nu een consistente workflow. Ik ontvang in een mum van tijd feedback over de vraag of het programma al dan niet zonder botsingen kan worden uitgevoerd op de machine – en dat met bijna honderd procent zekerheid."
De ondersteuning door hyperMILL en de virtuele machine is belangrijk voor de productiespecialisten van DLR-RM, en dat niet alleen voor 5-assige freesbewerkingen. Ook het programmeren van het draaifreescentrum is een veeleisende taak, die wordt ondersteund door hyperMILL TURN-MILL Machining. Michael Dreer voegt nog toe: "Om ook hierbij maximale zekerheid te verkrijgen, hebben we ons beschikbaar gesteld als bètatester van VM voor het draaifrezen, dat nu superbetrouwbaar werkt."
Geautomatiseerde job-linking en BEST FIT
Naast NC-codesimulatie omvat hyperMILL VIRTUAL Machining ook de Optimizer-module. De Optimizer past het NC-programma tijdens het genereren van de NC-code naadloos en volledig automatisch aan de kinematische eigenschappen van de geselecteerde machine aan. Hierbij worden de in technisch opzicht beste positioneringen geselecteerd en geoptimaliseerde verbindingswegen tussen de afzonderlijke bewerkingen gegenereerd. Michael Dreer gebruikt de Optimizer voornamelijk voor job-linking: "Deze functie koppelt mijn afzonderlijke jobs aan veilige, geoptimaliseerde en botsingsvrije bewegingen, zonder dat ik me daarom hoef te bekommeren.”
Terwijl het productieteam van DLR-RM programmeertijd bespaart met de Optimizer, verkort de BEST FIT-functie, die als add-on voor hyperMILL VIRTUAL Machining beschikbaar is, de tijd die nodig is voor het opspannen en uitlijnen van de component. “Bij onze lichtgewicht constructies hadden we vroeger een verspaningsvolume van meer dan 90 procent, daarom laten we deze componenten nu waar mogelijk via 3D-metaalprinten of precisiegietwerk vervaardigen", legt Michael Dreer uit. "We moeten echter ook functionele oppervlakken, gaten en schroefdraden bewerken op deze onderdelen."
Een van de problemen bij de additief geproduceerde of gegoten onderdelen was het opspannen op de machine en het nauwkeurig uitlijnen ervan. Dit vereiste een gecompliceerde opspanning en een enorme hoeveelheid tijd, omdat ook de reproduceerbaarheid van vervolgonderdelen moest worden gewaarborgd. "Met BEST FIT hebben we een manier gevonden om dergelijke onderdelen snel en eenvoudig in te stellen en betrouwbaar te bewerken", aldus een opgetogen Harald Wagner.
Waar het bij BEST FIT om draait, is een intelligente uitlijning van de component in het CAM-systeem. Met andere woorden: de component wordt op de machine bevestigd zonder te worden uitgelijnd. "We gebruiken daarvoor bijvoorbeeld geprinte kunststof spanmiddelen die weinig kosten," vertelt Michael Dreer, "omdat het opspannen geen kwestie van millimeters is." Daarna wordt de component op de machine afgetast met een 3D-meettaster. De resultaten worden in de vorm van een meetrapport geretourneerd naar het CAM-systeem. Aansluitend verplaatst hyperMILL BEST FIT de CAD-component, zodat deze zich volledig in het gemeten ruwmateriaal bevindt.
"Ik kan dit controleren op het scherm, maar meestal past alles meteen perfect." Vervolgens past BEST FIT de NC-code aan, simuleert deze code ten opzichte van de werkelijke opspansituatie en optimaliseert automatisch het programma. Michael Förster, Senior Product Marketing Manager bij OPEN MIND, legt uit wat de volgende stappen zijn: "Om een veilige en nauwkeurige bewerking te garanderen, voert de machineconfigurator op dit punt een controlemeting uit. Als de positie op de machine overeenkomt met het geoptimaliseerde programma, kan het bewerken beginnen zonder dat de machineconfigurator tijd en moeite heeft hoeven steken in het uitlijnen van de component op de machine. De voordelen: enorme tijdsbesparing, betrouwbare bewerking en planbare processen."
Michael Dreer en Harald Wagner zijn het daar volkomen mee eens: "Dat bespaart ons zeer veel moeite. De investering in hyperMILL, inclusief de simulatietool VIRTUAL Machining en BEST FIT, heeft absoluut zijn vruchten afgeworpen. We kunnen nu sneller programmeren, we beschikken over een NC-codesimulatie die ons maximale zekerheid biedt en we kunnen onze geprinte componenten veel eenvoudiger instellen."